
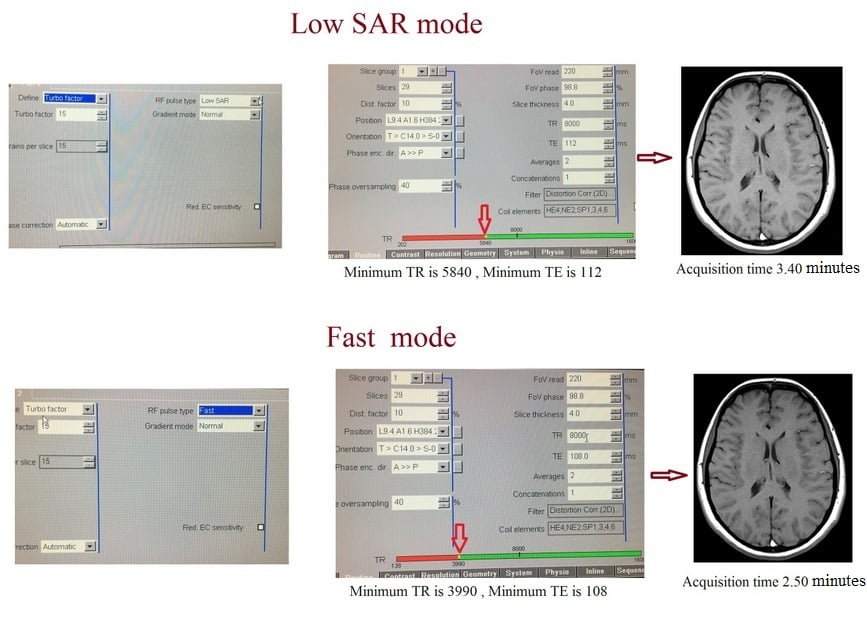
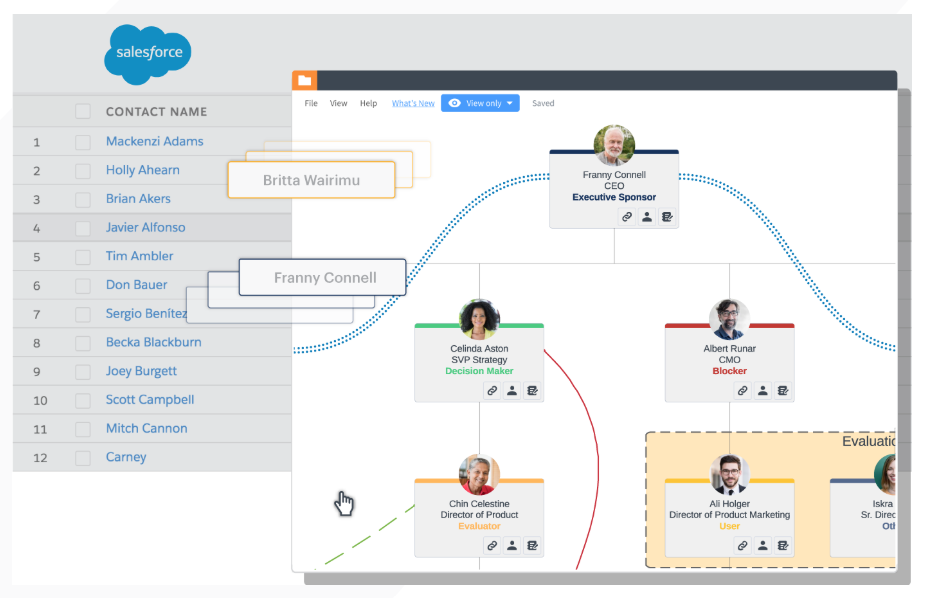
If you’re modeling a brand-new process, study whatever data is available, including standards for whatever is being produced in the process.ĭraw a draft diagram and confirm it with people involved in the process. Study the equipment, activities and relationships through observation and interviews. For a smaller, more basic process, you might do this yourself, perhaps even starting with sticky notes. For a sophisticated process, different versions of the diagram may be drawn to communicate with people in different roles.įor an advanced process such as at an industrial plant, the research may be done through a project team, quality control group or a consultant. P&IDs take the conceptual aspects of a PFD and add detail about the equipment, process sequence, process and utility piping, bypass lines, instruments, valves, vents, drains and other items.ĭefine the scope of your process to be studied and what you hope to gain.ĭecide on what level of detail is needed for your purposes. On the other hand, a Piping and Instrument Diagram (P&ID) is more technical, describing mechanical details for piping designers, electrical engineers, instrument engineers and other technical experts who need this detail more than they need process details. The process flow is usually shown from left to right, and arrows show flow direction. A rectangle is usually used to show a piece of equipment and labels illustrate function. Each block can depict a single piece of equipment or a stage in a process. These are also called Block Flow Diagrams and Schematic Flow Diagrams. When the diagram needs to show multiple unit processes at a plant, it becomes more of an overview, containing less detail. Typically, these more detailed items are omitted: Values often will include minimum, normal and maximum. Operational data: Such as pressure, temperature, density, mass flow rate and mass-energy balance.Control valves and process-critical valves.

Process piping: Moves the product, usually fluids, between equipment pieces.Examples include compressors, mixers, vessels, pumps, boilers and coolers. Major equipment: Including names and ID numbers.You can find a comprehensive list of standardized symbols with our PFD symbols guide.Ī typical PFD for a single unit process will include these elements: Our UML diagram tool can help you design any custom state machine diagram.The most common PFD symbols in use today come from agencies such the International Organization for Standardization (ISO 10628 – Flow Diagrams for Process Plants, General Rules), the German Institute for Standardization (DIN) and the American National Standards Institute (ANSI.) However, many companies use their own symbols, which are often similar but vary as they become more detailed. Below, you can see both these elements at work in a basic diagram for student life. Transitions are marked with arrows that flow from one state to another, showing how the states change. States are represented with rectangles with rounded corners that are labeled with the name of the state. State diagrams mainly depict states and transitions. Rather, they illustrate specific kinds of behavior-in particular, shifts from one state to another. However, despite having clear start and end points, state diagrams are not necessarily the best tool for capturing an overall progression of events. In order to understand the different states of an object, you might want to visualize all of the possible states and show how an object gets to each state, and you can do so with a UML state diagram.Įach state diagram typically begins with a dark circle that indicates the initial state and ends with a bordered circle that denotes the final state. States refer to the different combinations of information that an object can hold, not how the object behaves. A state machine is any device that stores the status of an object at a given time and can change status or cause other actions based on the input it receives.
